Barton Malow’s Virtual Design and Construction (VDC) team uses the latest technology and processes to capture valuable data on project sites to create 3D models from photographs or laser scans. These reality capture techniques greatly improve safety, quality, and productivity throughout the project lifecycle.
360 Photo and Video Capture
Rather than partnering with an expensive third-party vendor, Barton Malow leverages in-house 360-degree site photography to document in-wall conditions, above-ceiling conditions, and general jobsite progress during construction. Our high-resolution 360-degree cameras take panoramic images from various locations and during strategic phases of the project. This chronological series of images, linked to points in a plan view, can be shared with all project stakeholders via a web-based platform throughout the project lifecycle. As part of the closeout process, our image library is transitioned into a packaged format and delivered to the Owner with related critical project documentation.
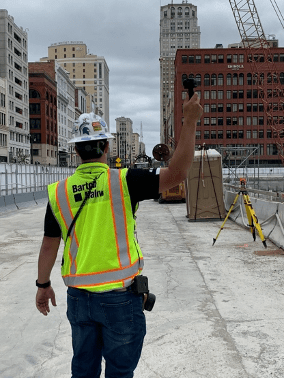
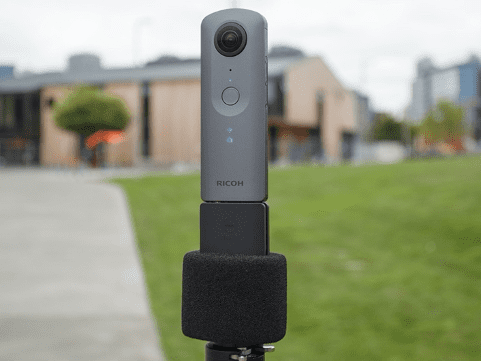
Drones
Drones, a growing technology, provide a variety of benefits throughout the entire construction process. Barton Malow uses high-resolution photographs and video footage to support site investigation, coordination, progress documentation, and QA/QC efforts. We also capture photogrammetry data that can be used in our 3D logistics visualizations. This data aides in accurate vehicular and pedestrian routes, material storage areas, and safety-related components of the job site.

Utilizing drone-mounted thermal cameras, we can investigate locations where air and moisture may be penetrating the exterior envelope. This minimizes the risk that may occur when crews are in potentially unsafe conditions and contributes to the performance quality of the building envelope.
The information and data from drone flights can be easily shared through BIM 360 with customizable dashboard applications like Drone Deploy. This easy access to the drone imagery and footage allows all project stakeholders to become aware of current site conditions remotely.
Laser Scanning
Barton Malow utilizes laser scanning to collect highly accurate details for real-world conditions, quickly and with minimal cost. This technology is especially effective for renovation and addition projects, as well as projects that have a high level of accuracy requirements for the As-Built BIM.
Documenting existing conditions in a 3D model environment ensures an efficiently designed and coordinated project. Laser scanning is a non-contact, non-destructive technology that captures existing 3D spatial conditions to a very high degree of accuracy. The scanning process results in millions of survey points, known as a point cloud, which can be overlaid in the 3D model environment to ensure all project stakeholders are coordinating with true in-field conditions.

Additionally, our construction trades utilize the point cloud data to maximize prefabrication opportunities and mitigate unplanned field-routing of building systems. This technology allows us to maximize quality and efficiency while working collaboratively with the design team in a familiar digital format.
Point-Based Layout
Prior to performing any work on site, Barton Malow plans and coordinates as much as possible in a virtual 3D environment. By building virtually first, problems are identified and resolved, and building information is purified so that it is constructible and reliable to construct from. Through planning effectively in the BIM environment, we leverage many value-added workflows to drive schedule and budget certainty throughout the project’s duration.

One of those workflows is point-based layout. We use sensitive surveying technology and equipment to effectively overlay project components from the BIM environment on the physical site. This helps us ensure accuracy and certainty that what we install is in physical alignment with what we virtually planned in the 3D model. Barton Malow applies this methodology to all our concrete, rebar, and civil self-perform work, as well as other strategic building systems to support installation and alignment by our trade partners.
These reality capture and integration activities help us discover, collect, and register data at the start of a project, and guide the creation of the 3D model used in the Building Information Modeling stage. Look for an upcoming series that covers Building Information Modeling (BIM) activities that help develop the project’s workflow, to collaboratively analyze and refine activities throughout the duration of the project.